Mastering the Craft: Best Practices and Applications of CNC Plasma Cutting
In the realm of metal fabrication, CNC plasma cutting stands as a beacon of efficiency, precision, and versatility. This powerful technology has revolutionized how industries approach the cutting of steel, aluminum, and other conductive metals, offering a blend of speed and accuracy that traditional methods can’t match. From intricate art pieces to robust industrial components, the applications of plasma cutting are as diverse as they are impressive. Let’s dive into the best practices for utilizing this technology and explore its wide range of applications.
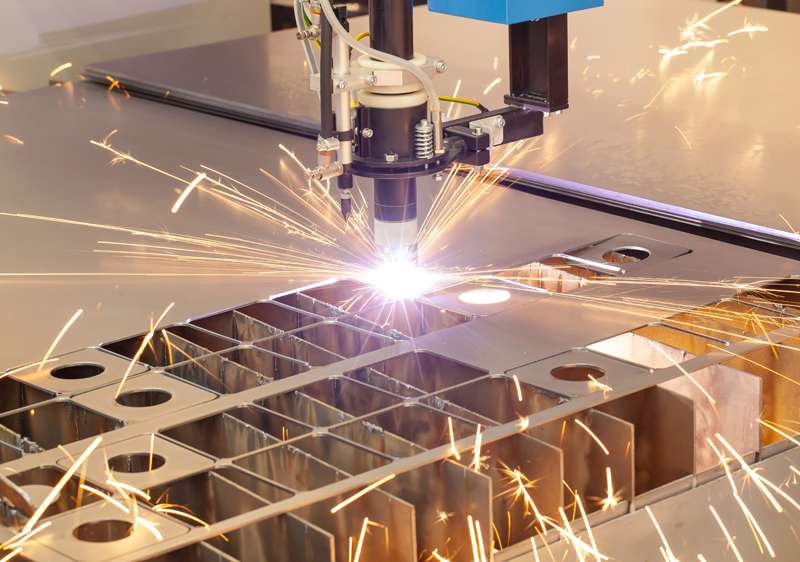
Understanding CNC Plasma Cutting
CNC custom plasma cutting is a process that uses a plasma torch controlled by a computer to cut through electrically conductive materials. It’s celebrated for its ability to produce clean, precise cuts with minimal heat input, making it ideal for a variety of materials including plasma cut steel and plasma cut aluminum. The process is not only efficient but also highly adaptable, accommodating complex shapes and designs with ease.
Best Practices in CNC Plasma Cutting
- Proper Material Preparation: Ensuring materials are clean and free of any coatings or residues is crucial. Contaminants can affect cut quality and increase wear on consumables.
- Optimal Cutting Speed: Finding the right speed for the material thickness is key. Too fast, and the cut may be incomplete; too slow, and the material may experience excessive heat input, affecting its properties.
- Correct Torch Height: Maintaining the correct torch height is essential for optimal cut quality. Modern CNC plasma cutting systems often include automatic height control to adjust for variations in material surface.
- Use of High-Quality Consumables: High-quality consumables not only extend the life of the plasma torch but also ensure consistent cut quality. Regular checks and replacements are necessary to maintain performance.
- Regular Maintenance: Like any sophisticated machinery, a plasma cutting service requires regular maintenance. Keeping the CNC machine clean and well-maintained ensures reliability and precision in the cutting process.
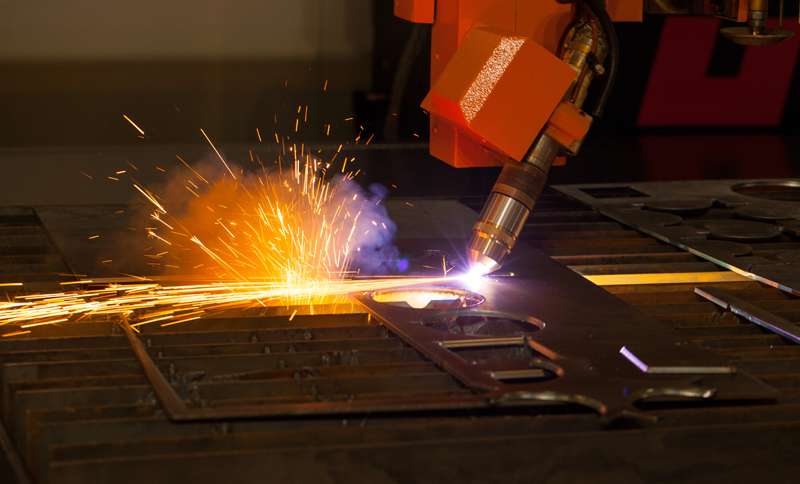
Fun Facts about CNC Custom Plasma Cutting
CNC custom plasma cutting is a process that uses a high-velocity jet of ionized gas delivered from a constricting orifice to cut through electrically conductive materials. The plasma is generated by electrically ionizing gas, which produces a high-temperature, high-velocity stream capable of melting and expelling material from the cut. Here’s an overview of the generation of plasma and the properties, including the temperature of the plasma, in CNC plasma cutting systems:
Generation of Plasma
Power Supply: The process begins with a power supply that provides a high voltage, direct current (DC) electric arc between an electrode and the workpiece (the metal being cut). This power supply is typically in the range of 100 to 400 VDC.
Gas Flow: A gas, often air, nitrogen, oxygen, or a mixture, is forced through a small nozzle orifice at high pressure.
Ionization: When the electric arc from the electrode comes into contact with this high-pressure gas, it ionizes the gas, creating plasma. The plasma arc is extremely hot and conducts electricity.
Arc Maintenance: Once the arc is established, the power supply maintains a constant flow of electric current through the plasma, keeping it hot and ionized.
Properties of Plasma
Temperature: The temperature of the plasma in a CNC plasma cutter is one of its defining features. Plasma temperatures can range from approximately 10,000°C (18,032°F) to over 30,000°C (54,032°F), which is hot enough to melt virtually any electrically conductive metal quickly.
Conductivity: Ionized gas becomes an excellent conductor of electricity, allowing the plasma arc to be sustained with relatively low voltage once it is initiated.
Velocity: The plasma jet is expelled at high velocity, which assists in blowing molten material away from the cut, creating a cleaner cut with minimal slag.
Density and Pressure: The plasma’s density and pressure are controlled by the cutting system to optimize the cut quality and speed for different materials and thicknesses.
ASIDE: Comparison of Plasma Properties to the Properties of a Sun Plasma, often referred to as the fourth state of matter, shares remarkable similarities with the substance composing the sun and stars. In CNC plasma cutting systems, plasma’s extraordinary properties—high temperature, conductivity, and velocity—allow for efficient metal cutting. Similarly, these properties are foundational to the sun’s energy production and the dynamic phenomena observed in solar physics.
Plasma’s utilization extends beyond cutting; it’s instrumental in Inductively Coupled Plasma (ICP) spectroscopy, a technique used for detecting metals at trace levels in various samples. This showcases plasma’s versatility in both industrial and scientific fields. For more insights into plasma’s applications in ICP, refer to this handbook on the plasma state.
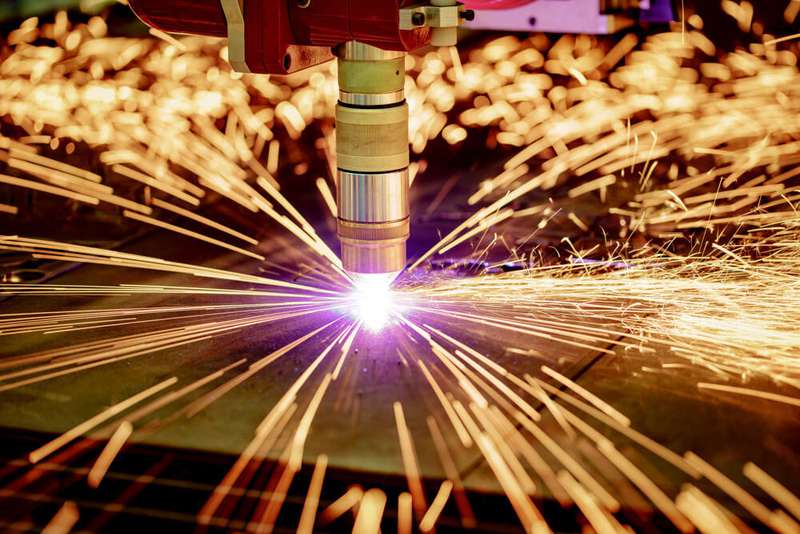
CNC plasma cutting systems harness the intense energy of plasma to perform fast, precise cuts on conductive materials, making it a valuable tool in many metal fabrication projects. The high temperatures generated by the plasma arc are a critical component of the system’s effectiveness, enabling it to cut through metal with ease. However, cutting with ease is not always the concern as much as precision and efficiency, so fabricators must also be concerned with cut quality to improve safety, reduce material waste, better material utilization via nesting, better match the intended design and component functionality, reduce secondary processing costs, enhance appearance, and improved tool life. For further detail on plasma cutting quality optimization refer to the article in The Fabricator.
Applications of CNC Plasma Cutting
The versatility of plasma cutting makes it suitable for a wide array of applications across various industries:
- Industrial Manufacturing: From components for machinery to structural frames, CNC plasma cutting is indispensable for creating precise parts quickly and efficiently.
- Automotive Industry: Custom fabricators rely on plasma cutting for creating intricate parts and custom modifications. Whether it’s for prototyping or production, plasma cut steel and aluminum are common in automotive workshops.
- Art and Decor: The precision of CNC plasma cutting allows artists and designers to create complex shapes and designs out of metal, opening up new possibilities for metal art, signage, and decorative panels.
- Construction: In construction, plasma cutting is used for cutting structural steel, piping, and sheet metal, facilitating quick assembly and installation.
- Shipbuilding: The ability to efficiently cut through thick plates of plasma cut steel makes plasma cutting a valuable tool in shipbuilding, where large sections of metal are the norm.
The following examples illustrate the broad utility of plasma technology across various industries, highlighting its importance in modern manufacturing, environmental management, and scientific research. Plasma’s ability to work at different scales and conditions makes it a versatile tool for solving complex industrial challenges.
- Plasma Display Panels (PDPs). Plasma technology plays a critical role in the creation of plasma display panels, commonly used in large TV screens. These panels contain millions of tiny gas-filled cells, or plasma cells, that emit light when electrically charged. PDPs are known for their deep blacks, wide color gamut, and superior viewing angles compared to LCDs, making them popular for high-end entertainment systems.
- Inductively Coupled Plasma (ICP) Spectroscopy is a powerful analytical technique used for the detection and quantification of elements in a wide range of samples. The process involves ionizing a sample with a plasma torch, which operates at temperatures sufficient to break down all molecules and atoms into their ions. ICP spectrometry can achieve high levels of detection sensitivity for almost the entire periodic table, making it invaluable in environmental monitoring, pharmaceuticals, metallurgy, and forensic science. Its ability to handle diverse sample types, from water to metal alloys and biological tissues, underscores the versatility and effectiveness of plasma technology in analytical chemistry.
- Plasma arc welding (PAW) utilizes a concentrated plasma arc to melt metal in the weld joint. This method offers greater precision and control compared to traditional welding techniques, making it ideal for applications requiring high-quality welds, such as in aerospace and automotive manufacturing.
- Surface Treatment and Modification modifies the surface properties of materials to improve adhesion, wettability, or corrosion resistance. It’s commonly used in the automotive, textiles, plastics, and biomedical industries to enhance the surface characteristics of materials, preparing them for painting, coating, or bonding.
- Semiconductor Manufacturing. Plasma etching and plasma-enhanced chemical vapor deposition (PECVD) are critical processes in semiconductor manufacturing. Plasma etching is used to precisely remove material from the silicon wafer to create microelectronic circuits, while PECVD is employed to deposit thin films onto substrates at lower temperatures than traditional CVD methods.
- Plasma sterilization is an effective method for sterilizing medical instruments and surgical equipment, particularly those sensitive to heat or moisture. Low-temperature plasma sterilizers use hydrogen peroxide or other gases to achieve sterilization, making them suitable for materials that cannot withstand conventional sterilization methods.
- Plasma Polymerization involves using plasma to initiate the polymerization of monomers into thin polymer films on various substrates. It’s used to create coatings that can provide waterproofing, biocompatibility, or other desired surface properties for a range of applications, from textiles to biomedical devices.
- Plasma Gasification is an advanced waste-to-energy technology that converts organic material into synthetic gas, heat, and electricity in an environmentally friendly manner. It’s capable of handling various types of waste, including municipal solid waste, hazardous waste, and even medical waste, offering a sustainable alternative to landfill disposal.
- Lighting. Plasma technology is used in lighting, most notably in plasma globes and plasma lamps. These devices create visually striking displays by generating plasma filaments from high-voltage electricity. On a larger scale, sulfur plasma lamps offer an energy-efficient lighting solution with a spectrum closer to natural sunlight than other artificial light sources.
- Material Synthesis. Plasma is used in the synthesis of materials, such as the production of nanoparticles and nanotubes. The high-energy environment of plasma facilitates the formation of these materials with unique properties, which are valuable in electronics, catalysts, and advanced materials science.
Conclusion: The Power of Precision
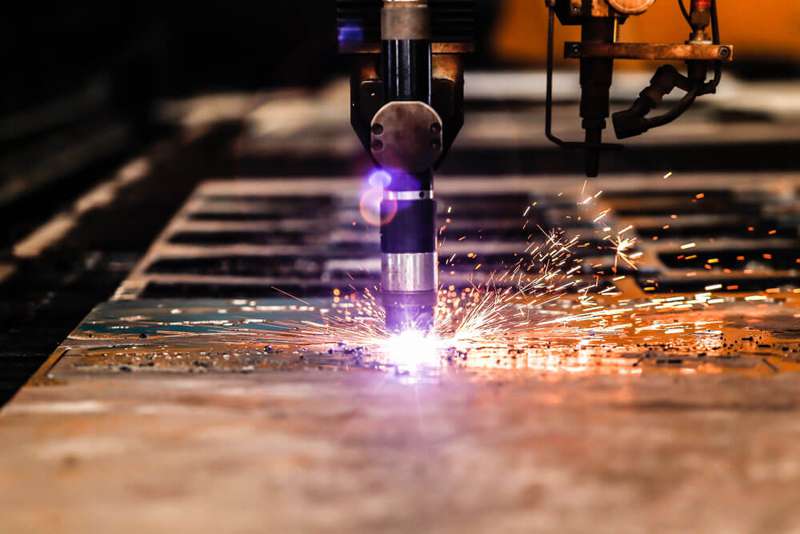
CNC plasma cutting is a testament to the power of modern technology to transform traditional manufacturing and fabrication methods. By adhering to best practices, businesses and hobbyists alike can harness the full potential of this technique, ensuring high-quality cuts across a variety of applications. Whether it’s through creating intricate designs in plasma cut aluminum for artistic projects or fabricating critical components for industrial use, the precision and versatility of CNC plasma cutting make it an invaluable tool in the modern maker’s arsenal.
As we continue to push the boundaries of what’s possible in metal fabrication, embracing technologies like CNC plasma cutting not only enhances operational efficiency but also opens up new avenues for creativity and innovation. With its wide range of applications and the ability to cut through materials with unparalleled precision, CNC plasma cutting is poised to remain a cornerstone of metalworking for years to come.
If you’re on the lookout for a plasma cutting company that boasts advanced machining and finishing services to seamlessly bring your innovative projects to life, don’t hesitate to reach out to us at techsup@emachineshop.com. We’re here to elevate your projects with unmatched precision, efficiency, and innovation, catering specifically to your custom plasma cutting needs. Whether you’re curious to learn more about our plasma cutting services, custom sheet metal fabrication, powder coating service, or require assistance with CNC milling or turning, we’ve got you covered. Already have a design that necessitates custom plasma cutting? Make your way to our quote page at https://emachineshop.com/quote to get started.